Сетевые протоколы управления
Внедрение контроля над предприятием посредством систем связи являлось главным приоритетным направлением приводной продукции Rotork в течение многих лет. Использование систем связи обеспечивает простоту, быстроту и надёжность ввода в эксплуатацию, а также дальнейшее отслеживание состояния предприятия.
Все приводы Роторк совместимы с большинством систем связи и автоматическими системами управления технологическими процессами, установкой соответствующей дополнительной платы. Привод передает данные о текущем состоянии по сетевому протоколу в АСУТП предприятия или в ПЛК и выполняет команды управления арматурой.
Наша собственная система Pakscan™ дополняет открытые системы от Foundation Fieldbus®, Profibus®, Modbus®, HART®и DeviceNet®. Новейшая технология наряду с экспертным знанием промышленных сетей гарантирует способность Rotork всегда предлагать идеальное решение для систем управления.
Управление по сетевым протоколам
Система Rotork Pakscan™ мировой лидер в автоматизации управления приводами арматуры и находится на переднем крае сетевых технологий с 1986 года. Сетевые системы Pakscan предоставляют пользователю непревзойдённый уровень управления, надёжности и поддержки. Техническая поддержка обеспечивается мировой сетью сервиса, чтобы Ваше предприятие работало 24 часа в день, 7 дней в неделю.
Современным предприятиям требуется самая последняя информация вплоть до уровня технологической установки. Руководителям предприятий требуются большие объемы информации и в более короткие сроки, чем прежде. Операторам технологических установок требуются полные возможности управления в любое время дня и ночи. Менеджерам по техническому обслуживанию также требуется информация для создания экономически выгодного календарного графика проведения профилактических и ремонтных работ. Для удовлетворения этих требований конструкторы прописывают требования по наличию протокола связи для обеспечения компьютерного контроля над каждым объектом и процессом на предприятии. Компьютеры решают задачи по обеспечению управления процессами и техническим обслуживанием путём обмена данными о состоянии оборудования и процесса внутри своей сети.
Система Pakscan предоставляет важную связь между приводом арматуры и системой управления. Система интеллектуальна, надежна, целостна, быстро и легко устанавливается в сеть между полевым оборудованием и комнатой управления. Она специально спроектирована для использования с продукцией Rotork. Благодаря высокой надежности
и эффективности, а также низким затратам на техобслуживание, сети Pakscan оказались непревзойденным лидером в области систем связи для приводов трубопроводной арматуры.
Большинство приводов Rotork возможно подключить к Pakscan использованием встроенной дополнительной платы. Другое оборудование возможно подключить использованием адаптеров Pakscan.
Полностью спроектированное решение
Автоматический контроль сети и устранение неисправностей
Отказоустойчивая промышленная сеть и резервное соединение с главным контроллером
Полностью запрограммированная мастер станция.
Экран для настройки (HMI) и встроенная клавиатура.
Связь с главным контроллером по Modbus RTU / TCP
Промышленная сеть проводная и/или беспроводная
Определённые время передачи данных и расстояние промышленной двухпроводной сети
Диагностика связи между полевым устройством и контроллером
Простое расширение
Возможность «горячего» резервирования
Настройка без необходимости использования подключения к АСУТП или ПЛК
Обширный опыт применения
Встроенный Web-сервер для полной диагностики системы
Управление по сетевым протоколам
Мастер станция РЗ
Мастер станция Pakscan P3 может управлять до 300 приводами, скомбинированными в проводной токовой петле и на беспроводной связи. Вариант исполнения P3 полностью резервированная Мастер станция с горячим резервом. Мастер станция Pakscan P3 оснащена местным интерфейсом пользователя, имеющим цветной дисплей, на котором отображаются состояния всех полевых устройств, текущий статус портов связи, аварийные сигналы системы, диагностическая информация, а также управление приводами и настройки. Простая 5-кнопочная панель предоставляет удобную навигацию по экранам дисплея.
Удалённый доступ к функциям управления активами осуществляется через встроенные веб-страницы, а также местный интерфейс пользователя предоставляет возможность управления, настройку, состояние и диагностики. Информация для управлении активами включает в себя историю журнала команд мастер станции, анализатор связи с главным контроллером, автоматическое оповещение об аварийных сигналах через электронную почту и регистрация данных для мастер станции и управляемых устройствах. Безопасность веб-сервиса обеспечивается обозначенным IP- доступом, https (безопасные веб-страницы) и защитой паролем.
Два последовательных и два Ethernet порта для связи главным контроллером позволяют обеспечивать резервированную связь. Предварительно сконфигурированная база данных Pakscan и обширный опыт работы с интерфейсами обеспечивают интеграцию с любой централизованной системой по Modbus.
Полевая мастер станция РЗ
Полевая Мастер Станция PakscanP3 (P3F) расширяет серию P3 предоставляя возможность установки мастер станции в непосредственно рядом с технологическим процессом. Установленная в защищённом от воздействия окружающей среды IP65 корпусе, она предоставляет (через АСУТП или ПЛК) управление и контроль 32 устройствами используя серийную или TCP / IP связь по Modbus. Настройка выполняется использованием встроенных веб-страниц.
IN-VISION — Эффективный,удобный в использовании
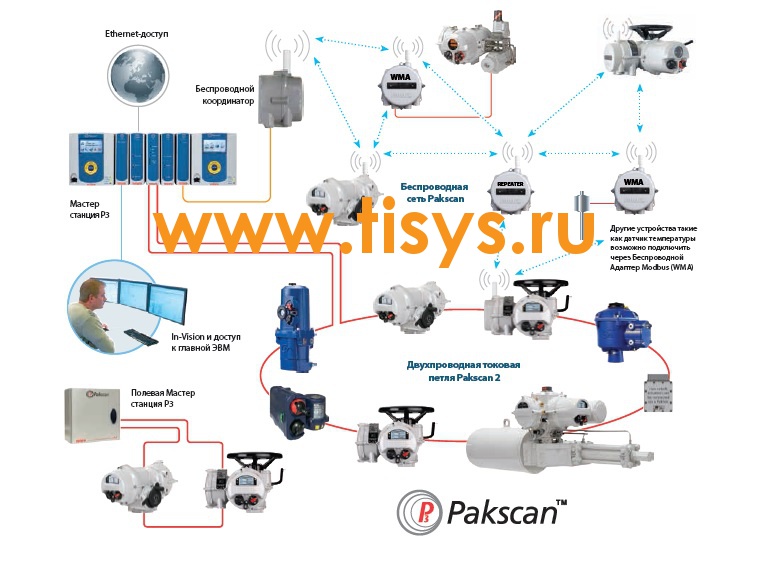
In-Vision представляет собой программное приложение автоматизированной системы управления и сбора данных SCADA для полного и удобного пользователю управления комплексными установками, такими как резервуары для хранения нефтепродуктов,установками для водоподготовки, которые могут иметь большое количество приводов и технологических сигналов для контроля и отображения. Работая с Pakscan и управляемая на стандартном ПК, In-Vision предоставляет ряд весьма универсальных графических дисплеев и средств управления, позволяющих руководителю производства просматривать и управлять всеми параметрами технологического процесса, при этом стоимость данной системы намного меньше по сравнению с другими системами.